Last month, I wrote about a day in the life of our new W56 delivery truck and the impressive results from a recent pilot. Several industry colleagues sent me a note saying, “how did the W56 do that?”
My response, “we designed it that way.” I wasn’t being satirical. Let me explain.
The majority of Class 5/6 delivery trucks on roads today are actually built on internal combustion engine (ICE) chassis that are retrofit, or “repowered,” with an electric motor replacing the engine. ICE chassis weren’t designed for high-torque electric motors. Significant modifications are required to ensure the motor is secure in a place it was not designed for, and that power is efficiently transferred to the wheels through a drivetrain it was not designed for. Battery packs that provide adequate range will take up space. The ideal location is between frame rails. However, this is not what an ICE frame was designed for. This can result in batteries placed outside the frame rails, which is not optimal. And as the frame wasn’t originally designed for battery weight, often times the payload capacity of repowered trucks is reduced.
As an aside, the manufacturer supplying the chassis will often require an ICE engine be purchased with it, which is then resold to internally combust in another vehicle.
Using a mix of proven and innovative design elements, the W56 was designed from the ground up to be a commercial EV. Here is a breakdown of how the design of the W56 delivers these no-compromise capabilities.
E-axle driven: Having 760 lb-ft of peak torque directly from the rear axle not only makes getting uphill and in and out of traffic a breeze, but also frees up space for batteries to be safely housed between the frame rails.
Frame designed for a CEV: The high-strength steel ladder frame with 120 KSI frame rails is engineered to carry battery weight without sacrificing payload. The design also ensures that everything needed for service is easy to get to.
Improved visibility and a quieter cabin: With no motor up front, the cabin is quieter and the lower front fascia greatly improves lateral and downward visibility compared to a repowered vehicle with a higher fascia that was required to accommodate an engine.
Lightweight walls – Innovative wall panels use lightweight composites and aluminum extrusions, providing strength and durability where needed, and reduced weight where it can be afforded. Free of rivets, the outer walls are smooth, providing for more visually appealing branding, while removing the risk of rusting or leaking rivets.
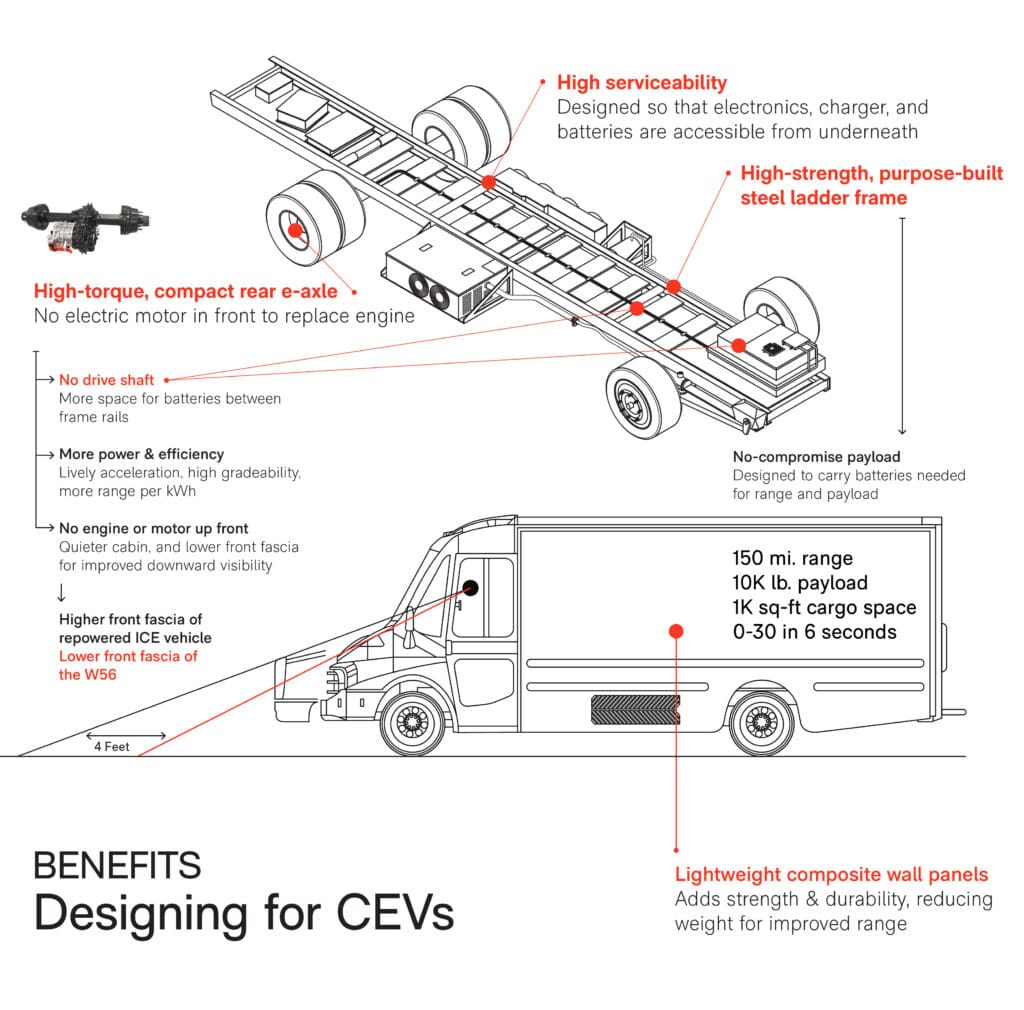
This is, of course, a very high-level view of the major benefits of a purpose-built design. Our engineering team made thousands of design decisions around these features, all based on their decades of designing both electric and ICE vehicles. But with the majority of vehicles in this class requiring well under 100 miles of daily range, and having ample time for overnight charging, the W56 outperforms both ICE and repowered vehicles in power, torque, safety, comfort, and maneuverability.
Continue reading about a real-world demo of the W56 in our blog post, Breaking Barriers: The W56’s Electrifying Performance.
The best way to appreciate the W56 is to drive one, and we have vehicles in production and available for delivery now. Contact us to begin your zero-emission today.